Occupational Health
KPO continues to work on the implementation of all possible measures to ensure Occupational Health at worksites and promote a healthy lifestyle. Due to COVID-19, we had to adjust our plans with respect to certain programmes and routine activities.
Tab. 7. Our targets in health protection
Our 2020 targets |
Target achievement |
Actions taken in 2020 |
Targets for 2021 |
Continue with the implementation of the Workplace Health and Well-being programme, which include:
|
Partially completed |
Stress Resilience Programme: several offline sessions had been held before the pandemic broke out. The programme was subsequently suspended, although the facilitators were able to conduct online sessions. Preparations for the Employee Assistance Programme had been ongoing: the tender was held and the contract for services was effectively signed. The programme “Something is wrong with me” was postponed to 2021 as the staff had been overloaded during the COVID-19 pandemic. |
Continue with the implementation of the Workplace Mental Health and Well-being including:
|
Continue with the setting up of the Committees for the “Care for People” Programme in other departments of the Company |
Not completed, revised |
Due to the COVID-19 pandemic, the planned work was suspended. At the same time, regular inspections of sanitary and living conditions at the facilities of contractors were carried out within this programme. |
Proceed with routine and unscheduled inspections of sanitary and living conditions at the contractors’ facilities
|
Based on the results of the pilot project, implement a Fatigue Risk Management Programme in other departments of the Company |
Postponed to 2021 |
We could not fulfil the tasks set for 2020 due to the COVID-19 pandemic. We had been working on the reduction of employee fatigue risks as part of adaptation to pandemic and quarantine conditions. |
Implement the Fatigue Risk Management Programme in other departments of the Company |
|
Not completed |
Actions planned for this task were not implemented due to the COVID-19 pandemic. |
Consider changing the concept of this programme in the context of current restrictions |
Complete the programme for installation of automated external defibrillators (AEDs) programme |
75 % completed |
|
Install 10 AEDs |
Introduce an Electronic Pre-shift Medical Examination System (EPMES) |
New task; 25 % completed. |
|
Purchase five units and install them at all KPO sick bays |
Consider hiring an expert to help with the implementation of International Occupational Hygiene standards. |
Cancelled |
No action is taken due to the COVID-19 pandemic. This task has been cancelled and is not further considered. |
|
Conduct an audit of the implementation of the Legionnaires’ disease risk reduction plan |
Partially completed |
The planned audit was cancelled due to the COVID-19 restrictions. |
Consider conducting an audit of the implementation of the Legionnaires’ disease risk reduction plan taking into due account the epidemiological situation |
OCCUPATIONAL HEALTH SERVICES
The Occupational Health function in KPO is carried out by Occupational Health and Hygiene Section. It includes a certified Occupational Hygiene laboratory, as well as an Occupational therapist and feldshers. The roles of the section include, but are not limited to:
- Health risk assessment,
- Occupational hygiene monitoring,
- Food and drinking water safety control,
- Medical examinations to determine fitness for work,
- Clinical examination of employees,
- Promotion of a healthy lifestyle (health awareness).
Occupation Health & Hygiene Section’s activity is guided by a number of procedures. Occupational health & hygiene specialists regularly undergo advanced training, including training as per international standards. The quality of service is also assessed by periodic audits by the Partner Companies and as part of ISO 45001 certification audits.
IMPROVING THE QUALITY OF EMERGENCY CARE
The 2020 HSE Improvement Plan included measures to improve medical evacuation capabilities (Medevac). In September 2020, KPO and the contractor, Astana Business Aviation Company, signed a joint Medical Evacuation (MEDEVAC Helicopter) Plan.
Fig. 8. Medical support indicators, 2020
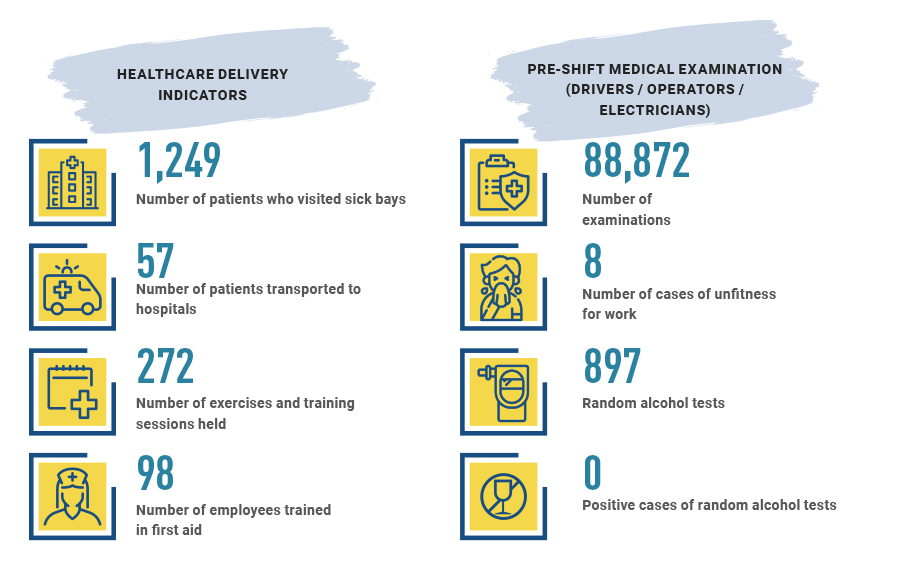
Health Department activities during the COVID-19 pandemic
In 2020, most of the Health Department’s efforts were focused on controlling the spread of COVID-19, preventing employees from being infected en masse and keeping the production running. The work was carried out in two directions: inwardly within the Company and outwardly in the region as a whole by supporting the community.
The following measures were taken to prevent our workers from falling ill en masse:
- people were moved to remote work pattern in order to minimize the office footprint,
- social distancing rules and a mandatory mask regime were adopted at all KPO facilities,
- all employees were provided with personal protective equipment (disposable masks and gloves, hand sanitation products),
- a regular PCR testing programme was implemented for all employees with an immediate isolation of people tested positive and their close contacts. Between July and December 2020, about 28,000 PCR tests were conducted, with 1,329 company employees being monitored and 2,874 employees identified as close contacts of confirmed cases of COVID-19.
- at the peak of the virus spread, an ‘Special Operators Group’ was set up from among the personnel of KPO Main Control Rooms. The group members had been designated to work by a specific work pattern and lodged at a third party accommodation block during their off work hours being isolated from the rest of the field staff and their families.
- a quarantine centre was set up in one of the Czech Camp accommodation blocks for a mandatory 14-day quarantine by expatriate employees arriving from abroad. This facility helped to ensure the continued availability of expatriate employees. Further, this facility was subsequently refurbished into an inpatient clinic to provide the required medical care to KPO employees in case of illness, as well as to alleviate the burden on local hospitals in the Burlin District. The inpatient clinic has 50 single rooms and 5 intensive care beds. It is fully equipped with all the essential medical equipment and personnel. In 2020, 20 KPO employees were successfully treated there.
- General Services Specialists, security guards and drivers received training on COVID-19 safety measures and compliance with sanitary and epidemic requirements.
- KPO Occupational Hygiene Laboratory specialists carried out the disinfection in workplaces. Also conducted awareness sessions on measures to prevent COVID-19, training, audit and inspections at the facilities of KPO and contractors on the implementation of the sanitary and disinfection arrangements. Public Health officers, together with KPO General Services, regularly monitored the main protective measures against COVID-19 (wearing masks, social distancing, hand sanitizing, etc.) at catering facilities, offices, transport, and production facilities.
- A COVID-19 Call Centre was established to consult the infected employees and their close contacts, as part of the measures aimed at preventing COVID-19. The Call Centre team included the Health Department’s staff members and volunteers from other departments.
- An internal hotline #2525 has been launched since the summer of 2020, which can be contacted by any employee regarding the COVID-19. The team members have been contacting people with confirmed COVID-19 and monitoring their health on a daily basis. They also supported with PCR testing for KPO and contractors’ employees, maintained the database and tracked the incidence rate.
- A dedicated COVID-19 page was launched on the KPO Intranet portal. It contains updated information on the COVID-19 situation in the Company, the country and the world; it also shares about preventive measures and provides answers to frequently asked questions about COVID-19.
Helping local community during the COVID-19 pandemic
Considerable efforts were made by the Company to support the state healthcare system.
High-tech artificial ventilators from Drager, two ambulances based on Lada Largus, two PCR laboratories and consumables for those, 5,000 disposable anti-plague suits and medicines were purchased for Aksai Central Hospital. KPO General Services rented a two-story building for the COVID-19 treatment to the local communities. This building was converted into an infectious diseases’ isolation facility fit to all the relevant medical requirements. The building houses comfortable double rooms with all the necessary amenities. All patients and medical personnel are provided with three hot meals a day at the expense of the Company. In addition, KPO provided a one-story building for a quarantine hospital for citizens of the Republic of Qazaqstan crossing the border with the Russian Federation. KPO has received a lot of positive feedback about the functioning of the above facilities.
The Akimat of Burlin District highly appreciated the Company’s support, which was both timely and comprehensive amidst the conditions of the COVID-19 outbreak in the Burlin District.
Moreover, a total of 29 ventilators, 20 oxygen concentrators, 10 bedside monitors, 20 infusion pumps and 20,000 reagents for PCR analysis were purchased for Uralsk hospitals.
Aksai Hospital Intensive Care Unit Upgrade Project
Since the end of 2019, KPO has been implementing the five-year Aksai Hospital Intensive Care Unit Upgrade Project. The main goal of this social project is to improve the Aksai hospital’s capabilities in administering medical emergency response, surgical treatment and intensive care that would meet international standards. Upon the Project’s completion, the hospital will be able to apply for international accreditation.
The project consists of the two phases:
- Upgrade of the existing units of Burlin Central Hospital in Aksai: admission unit, intensive care unit and surgery unit. It is planned to expand and renovate the admission unit, to replace the old equipment with the brand new ones, and to purchase an ambulance – a mobile intensive care unit.
- Employ doctors, foreign specialists with medical accreditation in the Republic of Qazaqstan to train local specialists and transfer international expertise in medical emergency care and surgery.
By the end of 2020, the project’s positive impact had already been acknowledged in terms of actual health indicators, such as the surgical mortality rate, which had reduced from 34 % in 2019 to 14 % in 2020. New methods of anaesthesia had been introduced, which made it possible to minimize the time spent by postoperative patients in the intensive care unit from 8 to 2 hours, which significantly reduced the cost of treatment.
The success was hugely acclaimed by the hospital’s medical staff and the local communities through social media. The project is still ongoing.
MANAGEMENT OF ILL HEALTH
KPO employees are provided with voluntary medical insurance valid on the territory of the Republic of Qazaqstan. Health insurance covers a range of services, from outpatient care to inpatient care and reimbursement of medicines and dental services.
Since 2019, the insured workers have an option of choosing their health care provider, and unused insurance funds can be shared among family members.
Absenteeism monitoring
In 2020, due to the COVID-19 pandemic, the absence of KPO employees for health reasons slightly increased compared to previous years.
Graph 1. KPO absenteeism rate, 2014–2020
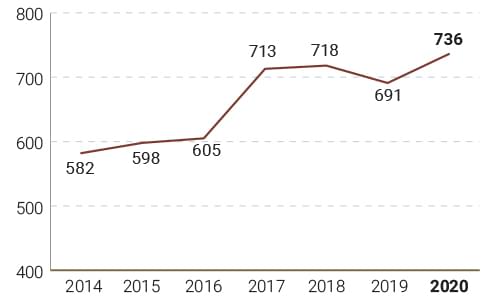
Note: KPO uses the following method to calculate the absenteeism rate:
- Absenteeism rate = actual number of days lost due to absence from work (due to illness) x 100/total number of employees. No information about the days of absence from the workplace for other reasons is available.
- KPO has adopted a methodology for calculating absenteeism by the number of employees (but not man-hours), since this methodology is a regulatory requirement.
Occupational diseases
We at KPO are conscious that the oil and gas industry is an operation inherently and innately associated with a number of hazards, such as hydrogen sulphide, chemical reagents, noise and vibration, climatic factors, biological and psychosocial factors.
It is therefore our key priority to identify these hazards, assess their potential impact on our employees and mitigate the risks. Examples of this include health risk assessments, certification of units and facilities for working conditions, and Occupational Health Monitoring programme.
From 2017 to 2020, no occupational diseases have been registered at KPO.
In 2020, health risk assessment was carried out mainly upon request and included an assessment of the workplace ergonomics.
Fitness to work
Since operation involves the exposure of workers to occupational hazards, it is very important to run medical examinations that help to determine fitness for work. In KPO, this service is provided by Contractor, which has all the permits for this type of activity.
In 2020, regular medical examinations were suspended due to the lockdown that started early April. At the same time, pre-employment medical examinations were carried out with the observance of precautionary measures. In September 2020, when the restrictions on the work of clinics were lifted, regular medical examinations of the Company’s employees were resumed.
In addition to mandatory medical examinations for field workers, the Company arranges free wellness checks for office personnel. This screening helps to determine a person’s health status and detect diseases at an early stage. The results of these examinations are not available to the employer and not used to determine fitness for work.
PROMOTION OF HEALTHY LIFESTYLE
In 2018–2019, KPO has implemented several Employee Mental Health and Well-being Programme tools to help workers improve quality of their life and work. KPO Stress Resilience programme launched in 2019 provides for direct interaction between the facilitator of the group and its members, therefore, in 2020, it was suspended during the initial COVID-19 quarantine. However, some participants found the opportunity to continue their sessions online! Their experience will, undoubtedly be used in the future, regardless of the situation with the pandemic.
In 2020, we had been preparing to introduce the Employee Assistance Programme. This programme intends online support and offline consultations. This programme was introduced in April 2021.
The programme “Something is wrong with me” was postponed from 2020 to 2021 due to the COVID-19 pandemic. This programme is similar to the programme introduced in Shell, one of KPO’s Parent companies.
Care for People Programme
The COVID-19 pandemic has also had an impact on the implementation of the Care for People Programme. Despite this, we, together with other departments of the company, have conducted regular inspections of the sanitary and living conditions of contractors. This was certainly of great importance, especially given the tense environment at the Company with the increasing number of COVID-19 cases.
Fatigue Risk Management Programme
Many employees of the Company and contractors were forced to stay at work longer than provided for by their rotation schedule due to strict self-isolation rules and associated migration restrictions in most countries of the world. In addition, the majority of shift personnel were temporarily transferred to an extended shift pattern: 14/14 days instead of 7/7 or 28/28 days instead of 14/14 and so on. All this could not but have an impact on the fatigue risk. Various measures were used to minimize the consequences, including scheduled time off, a remote work, a shorter working day, and additional manpower mobilization.
OPERATIONAL CONTROL OF INDUSTRIAL FACILITIES
KPO regularly monitors the Occupational Health and Hygiene at units and facilities. Table 8 shows the monitoring data for the last three years.
Tab. 8. Monitoring of physical factors in 2020
Occupational hazards |
2018 |
2019 |
2020 |
|||
No. of measurements |
No. of non-conformances |
No. of measurements |
No. of non-conformances |
No. of measurements |
No. of non-conformances |
|
Noise |
400 |
93 |
440 |
114 |
398 |
110 |
Vibration |
69 |
14 |
78 |
25 |
63 |
15 |
Electromagnetic fields |
3,888 |
44 |
4,164 |
36 |
3,500 |
35 |
Electrostatic fields |
2,129 |
0 |
2,322 |
0 |
1,737 |
0 |
Lighting |
2,879 |
815 |
3,085 |
703 |
2,861 |
660 |
Microclimate |
6,522 |
336 |
6,630 |
502 |
5,670 |
430 |
Workplace air |
14,595 |
0 |
15,471 |
0 |
11,607 |
0 |
TOTAL |
30,482 |
1,302 |
32,190 |
1,380 |
25,836 |
1,250 |
Noise exceedances are identified in production facilities, where the sources of noise are operating compressors, generators, material handling equipment, auxiliary equipment (ventilation units, air conditioners), etc. All these areas are used for non-permanent work, such as periodic taking of readings of measuring instruments and maintenance of equipment.
To minimize the impact of noise and protect the hearing organs of employees, since 2012, KPO has been operating a Hearing Conservation Programme, which includes informing employees about areas with high noise levels, providing PPE, “protection by time” or the minimum possible time to be spent in such areas including breaks, and timely maintenance of equipment. All production areas, which have noisy equipment, are marked with warning signs, equipped with noise maps, and work is performed with the obligatory use of PPE for ear protection.
KPO regularly upgrades lighting systems at its facilities. In 2020, KPO continued a phased replacement of fluorescent lamps to LED lamps that have more efficient light output.
Workplace attestation
Attestation of production facilities to evaluate working conditions was performed at Production Laboratory, Gathering and Drilling Rigs. Sixty-seven workplaces were evaluated. Corrective action plans were prepared following the outcomes of the attestation and submitted to the responsible persons for further actions