Operations and Development Projects
OVERVIEW
The Kazakhstan Branch of Karachaganak Petroleum Operating B.V. (KPO) is an international oil and gas condensate company that carries out production and exploration of hydrocarbons in West Qazaqstan region of the Republic of Qazaqstan. On behalf of its parent companies Shell, Eni, Chevron, Lukoil and KazMunayGas, KPO is an operator of the Karachaganak Field, one of the world’s largest oil and gas condensate fields in north-west Qazaqstan.
The Karachaganak oil and gas condensate field (KOGCF) covers an area of over 280 km2 and is located in a remote environment with extreme continental climate. Karachaganak is a unique field with complex operating conditions. The field is some 1,600 m thick and very complex and unique with its top at a depth of around 3,500 m. The extracted hydrocarbons contain up to 4.5 % of highly toxic and corrosive hydrogen sulphide (H2S), as well as carbon dioxide (CO2) which can be highly corrosive in certain conditions.
According to the latest Reserves Re-Determination Report for the Karachaganak field (accepted by the RoQ State Reserves Committee (GKZ) on 17.11.2017), it is estimated that the Karachaganak Field contains some 13.6 billion barrels of liquids and 59.4 trillion cubic feet of gas, of which approximately 13.6 % of liquids and 12.9 % of gas have been recovered as of 2020
The Company annually invests the funds in the application of leading-edge technologies to maximize sustainable economic value and minimise environmental impact. The total investment in the development of the Karachaganak oil & gas condensate field since the signing of the FPSA in 1997 to 31.12.2020 has totalled over USD 27 bln. As of end 2020, 4,368 people worked in the KPO organisation.
KPO FACILITIES
Hydrocarbon production and processing occurs at the three major interconnected units: the Karachaganak Processing Complex (KPC), Unit 2 and Unit 3. Approximately 2,000 kilometres of pipelines make up the infield system linking the major facilities and allowing efficient flows of production from the wells and among the units. Amongst the facilities, there is an Early Oil Production Satellite (EOPS) and Eco Centre. An overall view of the facilities is graphically presented on the figure 3.
The transportation system operated by KPO includes the main export route for stabilised liquid hydrocarbons – Karachaganak – Atyrau Transportation System (KATS) with two pumping stations: one at KPC and the other at Bolshoi Chagan, and a receiving and storage facility in KPO Terminal in Atyrau. The other export route is the Karachaganak – Orenburg Transportation System (KOTS), which is used by KPO for transporting gas to Orenburg Gas Plant in the Russian Federation.
As of end 2020, 114 producing and 19 re-injection wells were online at Karachaganak, from a total well stock of 467 wells. In 2020, KPO well stock was increased by one new horizontal well compared to the previous year (467 wells in 2020 vs 466 wells in 2019). The COVID-19 pandemic has forced a temporary suspension of drilling activities and lead to the lower increase in well stock.
Fig. 3. Karachaganak facilities and products
Fig. 4. KPO export routes
OUR PRODUCTS AND EXPORT ROUTES
KPO extracts and processes stabilised and unstabilised liquid hydrocarbons, raw gas and fuel gas. The majority of hydrocarbons produced in the Karachaganak Field are exported to maximize net sales revenues.
In 2020, around 99.8 % of liquid production was sold as stabilised oil to the Western markets via the following routes:
- the Caspian Pipeline Consortium (CPC) pipeline,
- the Atyrau – Samara pipeline and further through the Transneft system.
The CPC pipeline delivers KPO oil to the Black Sea port of Novorossiysk (Yuzhnaya Ozereyevka), whereas the Atyrau-Samara pipeline is used to deliver oil to the Ust-Luga port in the Baltic Sea (see Fig. 4). The main export route for oil is the CPC – the pipeline with a highest netback cost. The Atyrau – Samara route is used as an insurance backup.
In 2020, KPO exported a record total 10.86 mln tonnes of stabilised oil, out of which 10.51 mln tonnes were sold through CPC. To maximize revenue, nearly 0.34 mln tonnes of oil were exported via the Atyrau-Samara pipeline, of which 0.19 mln tonnes were diverted from CPC to sell at a higher netback price. During the reboilers’ washing at KPC, liquids were delivered to Condensate SC`s refinery.
The gas produced from the Karachaganak Field is:
- re-injected into the reservoir to maintain reservoir pressure,
- sold as raw gas to KazRosGas LLP under the long-term Gas Sales Agreement,
- sweetened (i.e. cleared from H2S) to generate electricity for KPO facilities including Gas Turbine Power Plant and for local power distribution companies.
In 2020, KPO sold 8.9 bln m3 of raw gas to KazRosGaz for processing at the Orenburg Gas Plant. Considering the commissioning of the new 26” gas pipeline from KPC to Unit-3, the winter trial run for determining maximum throughput capacity of sour gas pipelines from Karachaganak to Orenburg Gas Plant was performed in December 2020.
From 17 September 2018, KPO ceased the delivery of unstabilised condensate to Orenburg in connection with completion of the Delinking Project. This allowed a revenue increase thanks to diversion of liquids from Orenburg to the CPC route and to the “Condensate” SC refinery.
OPERATIONS AND SALES IN 2020
In 2020, KPO produced 143.9 mln barrels of oil equivalent (BOE) in the form of stable and unstable liquids and gas. Gas production in 2020 reached 20,2 mln m3. To maintain reservoir pressure, KPO re-injected ~ 10.4 bln m3 of gas into the reservoir, a volume equivalent to about 51,3 % of the total gas extracted.
Tab. 1. Production in 2020
Description |
Unit of meas. |
2020 |
2019* |
2018 |
Total Production |
Mboe |
143.9 |
137.9 |
147.5 |
Total equivalent stable oil |
Kt |
10,941 |
10,147 |
10,953 |
Total gas production |
Mscm |
20,214 |
18,614 |
18,913 |
Gas Injection into a reservoir |
Mscm |
10,362 |
8,710 |
8,589 |
Sweet Gas for internal needs |
Mscm |
761 |
685.4 |
723.6 |
*Full turnaround year
Tab. 2. Sales in 2020
Description |
Unit of meas. |
2020 |
2019 |
2018 |
Total Sales |
Mboe |
139.4 |
134.7 |
143.5 |
Stable Liquids |
kt |
10,857 |
10,160 |
10,365 |
Unstable Liquids |
kt |
24 |
9.9 |
615 |
Raw Gas |
Mscm |
8,986 |
9,113 |
9,493 |
Sweet Gas |
Mscm |
90 |
89 |
95 |
* From September 2018 condensate deliveries to Orenburg Gas Plant were stopped. Condensate supply was made to the SC “Condensate” refinery only
POWER GENERATION
For production needs within the Karachaganak field, KPO generates electrical power at its own Gas Turbine Power Plant (further as GTPP). Generated power is transmitted to the own production units throughout the Field, which include Karachaganak Processing Complex, Unit-2, Unit-3, Gathering system, Eco Centre, Pilot Camp, and the Karachaganak – Atyrau transportation system covering the oil pumping station in Bolshoi Chagan and block valve stations 1-26.
Four turbines, three of which are dual-fueled, are installed and operating at the KPO Gas Turbine Power Plant. In addition, KPO supplies electricity for the needs of the Western Qazaqstan Oblast population with capacity of circa 42 MW in winter and from 27 to 42 MW in summer.
In 2020, the GTPP completed minor inspection of gas turbine generators (GTG) #2 and #4 as well as inspection (overhaul) of turbine #2 combustors. The unplanned overhaul of GTG #4 has lasted from October to May 2020 due to the defect identified in the course of the scheduled inspection, which has resulted in a complete stator rewinding. The activities took longer than expected also due to the COVID impact and delays in spare parts supplies.
Power export to West Qazaqstan Oblast
As part of the Karachaganak Field’s Final Production Sharing Agreement (Art.I, Section 1.1.), KPO generates and exports power to the West Qazaqstan Oblast.
KPO exports power to electricity suppliers such as AksaiEnergo LLP and Batys EnergoResursy LLP, who then supply the power to the end consumers in West Qazaqstan Oblast.
Throughout 2020, KPO exported power from 26 to 41 MW to the regional grid, while the total volume of power export to WQO equalled ~ 297 mln kW-h or 39 % of the total volume. The power export in 2020 was 10 % lower than in 2019 due to unplanned overhaul of the Gas Turbine Generator #4. Supply of power and fuel gas in 2018–2020 is presented in table 3.
Table 3. Supply of power and fuel gas, 2018–2020
Description |
Unit of meas. |
2020 |
2019 |
2018 |
Electrical power exported to West Qazaqstan, including: |
mln kW-h |
296.93 |
330.26 |
305.06 |
|
mln kW-h |
26.35 |
26.28 |
29.90 |
|
mln kW-h |
270.58 |
303.98 |
275.16 |
Use of fuel gas to generate power for West Qazaqstan, including: |
mln m3 |
99.35 |
112.06 |
101.82 |
|
mln m3 |
89.95 |
88.98 |
94.91 |
|
mln m3 |
9.40 |
23.08 |
6.91 |
In 2020, KPO used mainly own gas for power generation. Purchases of gas from the third-party supplier to generate power for the WQO needs made circa 10.4 % of the GTPP total gas consumption. Those purchases were made mostly during the unstable operation of the Fuel Gas Sweetening unit at KPC (5-339 area) in February and March of 2020.
In the reporting year, the Company did not face production losses as the impact from external electrical grids.
TURNAROUND
The KPO Shutdown strategy is focused on optimisation of production and minimisation of cost by extending intervals between shutdowns and reduction of actual shutdown durations whilst ensuring safe continuous operations and regulatory compliance.
In 2020, Unit 3 was the only unit to have a full turnaround. The annual maintenance on the compression and dehydration systems at Unit 2 was deferred until April 2021, in order to minimise the number of personnel on site during the COVID-19 pandemic.
In addition to the regular HSE control activities and to the standard COVID regulations, prior to and during the Unit-3 turnaround, KPO implemented a number of extra COVID mitigation actions to minimise health risks to staff onsite and to reduce the chance of an outbreak, which could affect KPO’s performance in due time. These mitigation actions included the following:
- Reduction of scope, such that staff numbers required were minimised.
- Additional and larger meeting rooms to improve social distancing during many face-to-face meetings that were required at the turnaround.
- Our contractors have minimised sharing of accommodation by their staff.
- KPO required that all staff completed an extra PCR-test on day 7 after coming on-shift. This was aimed at identifying, as early as possible, any asymptomatic staff working at Unit 3.
As a result, no positive tests were recorded at Unit-3.
A total of just over 185,000 man-hours were registered during the turnaround: these were completed with zero reportable cases. Other key HSE statistics included Level III HSE inspections – 723 inspections held with 178 findings.
Overall, the turnaround was delivered ahead of schedule, with 99 % of planned scope being executed.
INDUSTRIAL WASTEWATER MANAGEMENT
Managing the produced and industrial effluent water is one of the main challenges faced by KPO in the Karachaganak Field.
KPO’s water management strategy consists of implementation of a portfolio of interconnected projects aimed at removal of production restrictions in terms of produced water handling as well as ensuring personnel safety, asset integrity and environmental compliance.
In 2020, two projects out of the four planned were fully completed. In 2021, refinement and implementation will continue including development of a detailed design for a new improved caustic neutralisation unit (CNU). Due to the COVID-19 pandemic’s impact on the project, the CNU start-up was postponed from 2022 to 2023.
Project delivery on replacement of induced gas flotation vessels and a tilted plate separator required for treating process effluents from oil is expected by the end of 2022. At the moment of this Report’s preparation, the pandemic impact was insignificant; the activities are ongoing as per the plan with a sufficient flexibility in case of possible schedule variance. The vessels’ replacement is a primary input to asset integrity while the new facilities will have higher capacity important for pursuing KPO water management strategy.
Tab. 4. Industrial wastewater management projects in 2020
Project |
Business driver |
Status |
Note |
Construction of a new 10-inch wastewater injection line; |
|
Successfully executed |
More details are given further in Case Study 1 |
Removal of H2S from the waste water at Unit 3 |
Environmental compliance |
Successfully executed |
Jump over line for diverting the Unit 3 industrial wastewater to KPC was commissioned fitted with the H2S removal technology |
Start-up of a modified gasoline demercaptanization unit |
Safe operations |
Partially executed |
Implementation of the project will allow a 30% reduction of the spent caustic soda formation and its supply to the industrial waste treatment unit, mitigating the risks for personnel. Due to the COVID pandemic in 2020, the project start-up was postponed to the first half of 2021. |
Workover of the two water injection wells |
Production maintenance |
Partially executed |
Workover of the two absorbing wells was agreed to perform in a successive order, not simultaneously, so that experience and data obtained in the first well workover will lay a foundation for the maximum efficiency on the second well. Workover of the second well is scheduled for mid- 2021. |
CASE STUDY 1
CONSTRUCTION AND COMMISSIONING OF NEW INJECTION PIPELINE FOR INDUSTRIAL WASTE WATER
Context / short description:
The existing 6-inch wastewater injection line was a bottleneck for production enhancement. Being a single pipeline used for sending industrial effluents for injection to deep subsurface Polygon 2, this line was non-piggable and had pit corrosion traces. Cumulatively, that created risks to production sustainability and limited the overall synergy of other water management projects.
Goal:
Unlocking full potential of projects aimed at removing production restrictions, taking into account predicted peak volumes of associated produced water, as well as improving integrity of KPO operations in whole.
Solution / actions:
Construction of a new 10-inch industrial wastewater injection line using line pipes available at the Company’s warehouse, thanks to which the project was implemented in the shortest possible time.
Result:
Implementation of the project has allowed to:
- Fully unlock the potential of short-term projects aimed at enhancement of capacities of the existing industrial wastewater re-injection network.
- Increase in the total capacity of wastewater treatment at the Field units (compared with 2019, current by 30 % and expected by 50 % upon completion of the other debottlenecking projects) and remove wastewater treatment limitations to liquids production.
- Reduce potential asset integrity risks associated with the existing 6-inch wastewater injection line.
Ultimately, the new industrial effluents injection pipeline is aimed at sustaining the production process upon the end of the service life of the old 6-inch injection line in 2027
TECHNOLOGIES IN DRILLING
In 2020, KPO continued working on minimization of a negative impact from drilling and well services operations on the environment. As previously, we continued our path towards zero emission ambition and applied measures listed below to reduce greenhouse gas (GHG) emissions, and consumption of water and resources:
- Application of oil-based completion and stimulation displacement fluid instead of water.
- Post-stimulation milling of downhole hardware (balls and baffles), which previously was done with coiled tubing unit and fluid displacement motors, is now replaced with wireline milling/ wireline shifting of frac sleeves with the use of electrical devices, hence no contaminated fluid to dispose and no flaring.
- Use of highly efficient environmental friendly burners that minimize fall-out, where flaring is inevitable.
- Use of High Gas Volume Factor (HGVF) pumps during wells kick-off and clean up to reinject produced hydrocarbon in high-pressure production line instead of burning them on the flare during the clean-up phase of a new or worked-over well.
- Evaporation of produced water.
KPO continuously works on developing technology and innovations aimed at improving well operations performance. In these terms, the following was achieved throughout the year 2020:
- The new design horizontal gas injector well was delivered in 2020. It is theoretically capable to provide higher injection rates above 6 Mscm/d;
- One new oil producing well was provided to enhance production;
- New drilling technologies have been applied for the first time in the field, such as RFID activated circulation valve, which helped improving overall performance and efficiency of drilling operations.
- To achieve high quality of zonal isolation KPO engineers and our cementing contractor used a special light-weight cement slurry that was designed in 2019. The light slurry technology enables additional improvement opportunities allowing significant reduction of well construction time and cost.
FIELD DEVELOPMENT PROJECTS
As the Contractor to the Republic of Qazaqstan, KPO has an obligation to conduct all operations necessary to carry out the development and production of petroleum in the contract area in accordance with International Good Oil Field Practice
Following the completion of the Karachaganak Phase II Initial Programme in 2003, KPO has been funding and implementing the Phase II Maintenance Programme (Phase II M). This phase includes the further activities, such as drilling of new development wells, undertaking workovers on existing wells, upgrading production facilities and other projects required to maintain a high production level for the benefit of the Republic of Qazaqstan.
In 2014, in order to avoid the increasing gas-oil-ratio causing the existing facilities to become gas constrained, KPO developed a programme of production Plateau Extension Projects (PEP). The Plateau Extension Projects are comprised of:
- KPC Gas De-bottlenecking project aimed at increasing the overall KPC gas processing by expanding the gas handling capacity;
- 4th Gas Reinjection Compressor project aiming to increase the annual daily average volume of gas re-injected into the reservoir and improve reservoir pressure support;
- 5th Trunkline and Gas reinjection wells project upgrading the injection network capacity downstream of Unit 2 through installation of a new trunk line, and drilling and completion of new gas injection wells.
International Good Oil Industry Practices means the good, safe and efficient operations and procedures commonly employed by sensible and diligent operators in the international petroleum industry, mainly regarding aspects related to the use of adequate methods and processes for obtaining maximum economic benefit in the final recovery of reserves, for minimizing losses, for operational security and for environmental protection. This definition is given in the «Аgencia Nacional de Hidrocarburos, Hydrocarbon Exploration and Production Contract No. 09 OF 2008, la Cuerva».
PEP projects portfolio was maturing and developing over the years, resulting in start-up of the 5th Trunkline and Gas reinjection wells project in December 2019 with first of the three injection wells.
In 2020, the development projects continued progressing with notable achievements despite a challenging global environment caused by COVID-19 pandemic and all the associated limitations that were imposed on all business activities, such as procurement delays, Force Majeure declared by some vendors, limitations imposed on travelling for the projects execution team, limited presence on site, foci of pandemic among the personnel, and many others.
Extensive scope of work has been carried out on KPC Gas Debottlenecking project, namely Drizo and dehydration units, substation and piperacks have been completed achieving the mechanical completion. Pipeline and tie-in 108 went into operation in September 2020 mitigating loss of production due to Unit-3 turnaround. In March 2021, the project has been successfully completed. The start-up activities are ongoing with a plan to handover to Operations in Q3 2021.
The 4th Gas Reinjection Compressor project has made a significant progress during the year. Compressor unit has been installed on foundations and erection of compressor building is nearing completion. Construction of an 8.5 km pipeline from Unit 2 to KOTS has been completed. Piping erection, electrical and instrumentation works are progressing rapidly. The project is expected to reach mechanical completion followed by commissioning activities and start-up by Q4 2021.
Karachaganak Expansion Project
KPO continues development of the Karachaganak field via the Karachaganak Expansion Project Phase 1 (KEP1), scheduled in a phased manner. The KEP1 project will create additional value for the Karachaganak Parent Companies and the Republic of Qazaqstan by maintaining the stabilised liquid plateau through the provision of additional wells, process facilities and gas reinjection to manage the increasing gas oil ratio (GOR) of the field.
In December 2020, the Karachaganak Parent Companies have signed the agreement sanctioning the KEP1A Project. That was another major achievement representing a new milestone in the continued development of the Karachaganak Field, building further on the achievements of Karachaganak Gas Debottlenecking Project (KGDBN) and the Fourth Injection Compressor (4IC) Project. One of the KPO’s key priorities in execution of KEP1A is maximizing the Local Content aimed at growing the local contractors’ competitiveness. The project will also create job opportunities for Qazaqstani workers.
The KEP1A 5th Gas Injection Compressor (GIC) Project represents the first phase of the KEP1 scope and comprises of the 5th Injection Compressor and other associated facilities. The 5th GIC Project pursues the opportunity to utilise the available dehydration capacity installed by KGDBN in the Karachaganak Processing Complex to increase gas re-injection capacity and integrate its scope within existing systems, utilities and facilities. The integration philosophy creates synergies and reduces CAPEX exposure. In 2021, the project is scheduled to carry out Early Works, to initiate long-life items procurement and to start mobilisation of the engineering, procurement and construction contractor.
The 6th Trunkline and 3 Injection Wells Project, which was decoupled from the KEP1A programme in March 2020 as a result of a Subsurface Technical Review, has the objective to maximise liquid recovery by increasing the field injection area. The project will re-distribute injection gas into South West Frank area of the field for pressure support of nearby low Gas-Oil-Ratio wells and better reservoir management.
In November 2020, the 6th Trunkline project has successfully passed Value Assurance Review 3, and the Engineering & Procurement for flowline and trunkline scope has been started in Q1 2021.
DIGITAL TRANSFORMATION PROGRAMME
KPO see the digital transformation as a key lever of business to simplify and enhance processes and organization.
As part of the ‘Digital Qazaqstan’ Programme, KPO has developed a plan of its technological modernization and digitization. Our Digital Roadmap initially foreseen 11 different themes relevant to macro fields of interest, with some 30 different digitization projects. Digital roadmap will allow KPO minimize the paper-intensive processes and maximize the digital workflows. In the long-term, digitization is expected to be followed by further development.
In 2020, KPO has mainly focused on the following projects:
- Streamlining of documentation including massive introduction of digital signatures. Over 1200 digital signatures were issued to KPO managers and staff aimed at facilitating business processes including when working remotely.
- Production optimization through implementation of the Facilities KPI Monitoring system, update of DINO software, execution of a pilot project for exception based surveillance and initiation of the wells telemetry project. The aim is to increase the hydrocarbon production by raising system efficiency and facility utilization to exploit its potential.
- Critical equipment monitoring with the implementation of enhanced performance based condition monitoring on rotating equipment in order to increase rotating equipment availability and decrease the maintenance cost and duration, allowing focusing only on needed intervention.
- Warehouse Management including implementation of a barcoding system and update of EWM software; the aim is to increase efficiency in Warehouse management and stock reduction.
- E-Procurement with the definition, set up and implementation of a common electronic procurement platform for the major O&G companies in Qazaqstan supported by the PSA Authority. The project targets creation of the more efficient platform with transparent process and direct sharing of data with parties involved in the authorization process.
Besides, in liaison with the KAZENERGY Association, KPO has supported the Student Digital Fest contest having engaged students from major universities in Qazaqstan. The final stage of the contest was completed in February 2020.
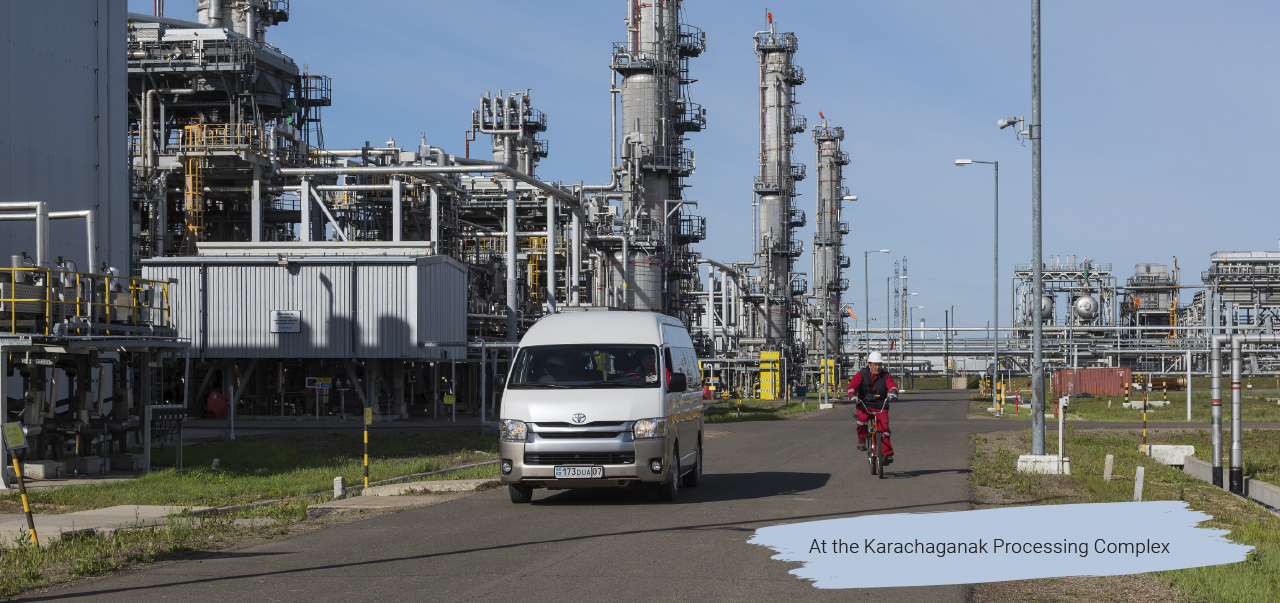