Safety
In order to minimize safety risks and impact of the Company, we have set a number of targets. The results of their implementation are presented further in the table
Our targets in 2021 |
Status |
Actions taken to implement targets in 2021 |
Targets for 2022 |
Continue implementation of the Safety Continuous Improvement Journey |
91 % completed |
The Plan was implemented through raising awareness on Life Saving Rules (e-learning) and consequences management, as well as, leadership and coaching, HSE competency assessments and management presence at work sites, procedures simplification. The name of the Plan was amended to highlight leadership. |
Continue implementation of the Safety Leadership Improvement Journey |
Complete competency assessments by 10 HSE elements for KPC supervisors |
100 % completed |
HSE Competence Assessment of KPO Supervisors has been completed. |
– |
Implement HSE Communication Plan for 2021 |
97 % completed |
The plan was implemented through raising HSE awareness, incentive mechanism, implementation programmes and campaigns, engagement meetings and workshops. |
Implement HSE Communication Plan for 2022 |
Implement Road Safety Improvement Plan |
90 % Completed |
14 out of 22 actions of the Plan were completed, the rest 8 actions are continued in 2022. See details in ‘Road Safety’ section. |
Obtain ISO 39001: Road Traffic Safety Management System Certification |
|
New Target |
|
Conduct assessments to understand the level of HSE Culture in KPO |
Why is it important to us?
Health, safety and asset integrity are the key elements for successful development and operation of any oil and gas condensate field. Safety of personnel in operations related to risks of H2 S, potential leaks and road incidents is of paramount importance for our Company. Our goals are that every employee is to come back home safe and sound and production leaks are entirely excluded.
KPO utterly commits to support effective HSE culture both internally and externally
HEALTH AND SAFETY PERFORMANCE
We plan our health and safety activities by tracking our progress and monitoring the world events. We measure our success in health and safety by frequency of incidents over a set amount of work in man-hours. Our health and safety records are presented for the period 2016 – 2021 with a focus on 2021.
Graph 1 demonstrates Lost Time Injuries Frequency (LTIF)2 and Total Recordable Injury Frequency (TRIF)3.
Graph 1. LTI and TRI frequencies: KPO and contractors, 2016–2021
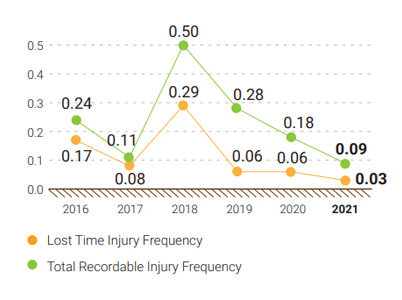
Note: KPO uses the following method to calculate LTI and TRI frequencies:
2Frequency of Lost Time Injuries (LTIF) = number of Lost Time Injuries (lost work day cases + fatalities) x 1 000 000 / man-hours
3 Frequency of Total Recordable Injuries (TRIF) = number of recordable incidents (lost work day cases + medical treatment cases + restricted work day cases) x 1 000 000 / man-hours)
In 2021, KPO TRIF made up to
In 2021, KPO LTI was
In 2021, the total number of recordable injuries in KPO reduced by half. The number of Lost Time Injuries decreased as well from two in 2020 to one injury in 2021. In 2021, LTIF was 0.03 (vs 0.06 in 2020) and TRIF – 0.09 (vs 0.18 in 2020). The main reasons for incident decrease are continuous implementation of the Safety Leadership Improvement Journey, completion of HSE Competence Assessment of KPO Supervisors, implementation of the HSE Communication Plan. We investigate all incidents to avoid reoccurrence. In addition, we share learnings from incidents with our contractors and other interested parties and adopt safety improvement practices from other companies.
Table 7 represents KPO LTIF versus contractors LTIF for the last three years. KPO and contractors’ data are presented separately. To obtain a consolidated indicator, a calculation formula should be applied, and not just a summarized data used.
Tab. 7. Lost Time Injuries frequency: KPO vs contractors, 2019–2021
Performance Indicators |
2021 |
2020 |
2019 |
Lost Time Injury Frequency (KPO) |
0.14 |
0.00 |
0.13 |
Lost Time Injury Frequency (сontractors) |
0.00 |
0.07 |
0.04 |
Table 8 represents KPO TRIF versus contractors’ TRIF.
Tab. 8. Total Recordable Injury Frequency: KPO vs contractors, 2019–2021
Indicators |
2021 |
2020 |
2019 |
Total Recordable Injury Frequency (KPO) |
0.14 |
0.00 |
0.13 |
Total Recordable Injury Frequency (contractors) |
0.08 |
0.22 |
0.33 |
KPO strives to make work places safe. Despite this, during 2021 there were three incidents, resulting in various injuries of KPO and contractor’ employees.
Tab. 9. Incidents in 2021
Injury Type |
Description |
Number |
Lost Work Day Case |
Eyes injury (chemical burn) as a result of caustic soda solution release |
1 |
Total Recordable Injuries, where employee returned to work after medical treatment or was transferred to restricted work |
Forearm injury (cut) by sharp object |
1 |
Arm injury as a result of slipping and falling |
1 |
|
TOTAL |
3 |
No severe Road Traffic Incident (RTI) was reported in 2021. The RTI frequency per 1 million km driven remained zero in 2021 the same as in 2020. The zero rate is associated with the implementation of Road Safety Improvement Plan, driving competence assessment and other achievements as described in the Road Safety section.
In 2021, the kilometers driven by KPO vehicles amounted to 40.2 million km, compared to 37.9 million km in 2020.
Tab. 10. RTIF: KPO vs contractors, 2019–2021
Performance Indicator |
2021 |
2020 |
2019 |
Road Traffic Incident Frequency (KPO) |
0.00 |
0.00 |
0.00 |
Road Traffic Incident Frequency (contractors) |
0.00 |
0.00 |
0.03 |
Tab. 11. Fatality Frequency: KPO vs contractors, 2019–2021
Performance Indicator |
2021 |
2020 |
2019 |
Fatality Frequency (KPO) |
0.00 |
0.00 |
0.00 |
Fatality Frequency (Contractors) |
0.00 |
0.00 |
0.00 |
Graph 2. Frequency of severe RTI: KPO and contractors, 2019–2021
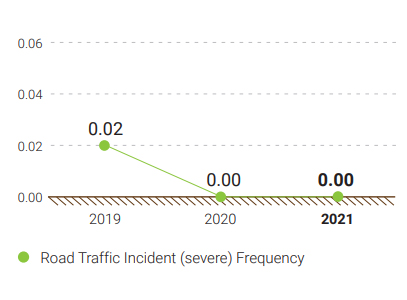
Graph 3. Fatality Frequency: KPO and contractors, 2019 – 2021
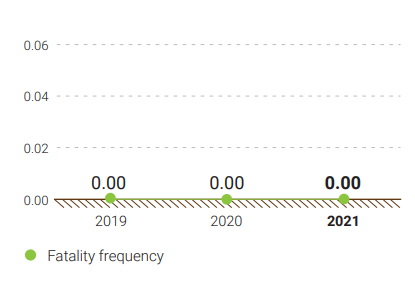
In 2021, KPO and сontractors’ employees worked 32,265,055 man-hours: 21 % of them (6,924,081 man-hours) worked by KPO employees and 79 % (25,340,974 man-hours) by сontractors’ employees.
Tab. 12. Man-hours worked: KPO vs contractors, 2019 – 2021
Indicators |
2021 |
2020 |
2019 |
Man-hours worked (KPO) |
6,924,081 |
7,269,825 |
7,829,313 |
Man-hours worked (Contractors) |
25,340,974 |
26,955,757 |
27,339,092 |
Total |
32,265,055 |
34,225,582 |
35,168,405 |
In 2021, only one high potential incident was recorded in KPO: process incident with asset damage.
Tab. 13. High Potential Incidents*: KPO vs contractors, 2019 – 2021
Indicators |
2021 |
2020 |
2019 |
High Potential Incidents (KPO) |
0 |
1 |
3 |
High Potential Incidents (Contractors) |
1 |
1 |
8 |
Total |
1 |
2 |
11 |
In 2021, 64 near misses were registered in the Company: of which 39 (61 %) were reported through the Incident Notification Procedure, and 25 (39 %) – through HSE cards. For each near miss same as for each incident, KPO performs a thorough investigation, identifies the immediate and root causes and develops recommendations to correct the shortcomings and prevent their recurrence.
Tab. 14. Near misses*: KPO vs contractors, 2019 – 2021
Indicators |
2021 |
2020 |
2019 |
Near misses (KPO) |
21 |
27 |
47 |
Near misses (Contractors) |
43 |
46 |
64 |
Total |
64 |
73 |
111 |
PEER COMPARISON
Every year we review our key safety performance indicators against the other O&G producers’ indicators reported by International Organisation of Oil and Gas Producers (IOGP). IOGP annually publishes HSE performance indicators on the website www.iogp.org.
In 2021, the number of Lost Time Injuries in KPO decreased (1 LTI in 2021 versus 2 LTIs in 2020). If compared with other peer companies in 2021, KPO LTIF is better than the performance of IOGP 10 top and IOGP average (see graph 4).
Graph 4. KPO Performance versus IOGP, 2008 – 2021
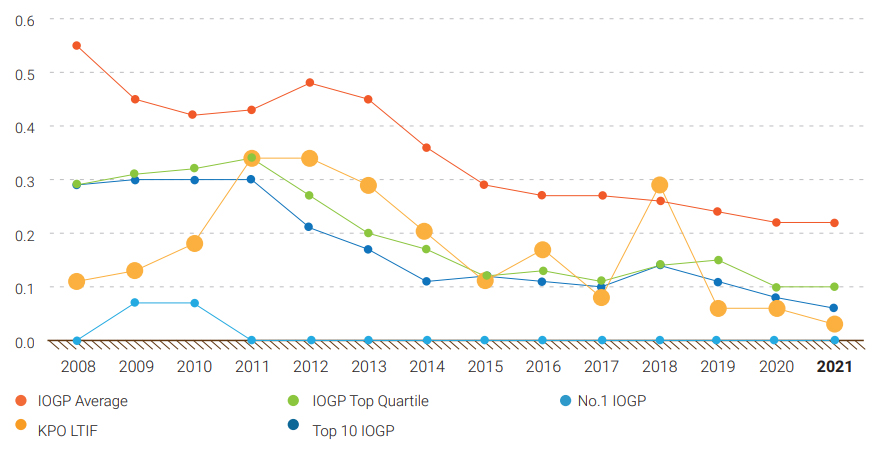
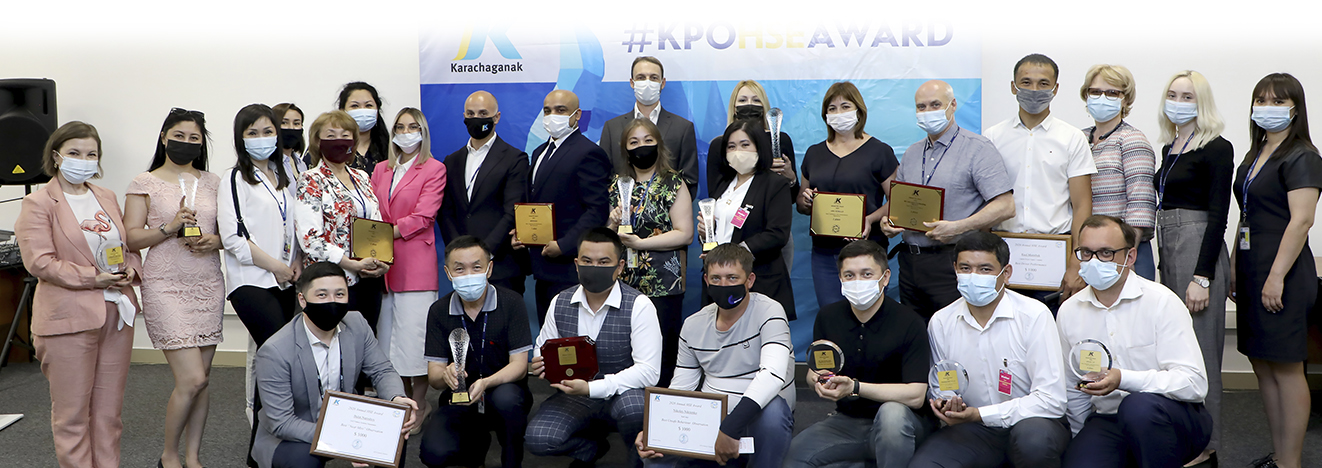
HSE IMPROVEMENT PLAN FOR 2021
The overall objective of KPO HSE Improvement Plan is to improve Health, Safety and Environment management, to further control risks and to prevent harm to people and the environment. This is done by implementing Key Focus Elements that are over and above KPO’s day to day business activities to deliver tangible benefits and improvements.
- In 2021, KPO has adopted a structured approach in preparation of the HSE Improvement Plan to ensure the Plan and the KPIs support each other and HSE objectives are achieved.
- 2021 KPO HSE Improvement Plan consisted of level I-II-III interlinked objectives:
- The subordinate plans were developed to address these objectives;
- All KPO stakeholders owned and shared objectives and subordinate plans;
- KPO worked together to implement the plans and strengthen the barriers, in order to achieve the common highest goal.
Monitoring of the Plan was arranged by means of Traffic Light system (Green, Yellow, Red) applied to Levels I, II and III.
In the following paragraphs, we present the activities of our Safety Leadership Improvement Journey and road safety. Environment protection, Asset Integrity, risk management and Health are presented in relevant chapters.
LEVEL I (main goal): |
No harm, no leaks |
LEVEL II (supporting goals): |
|
LEVEL III (how this will be achieved): |
Strategy and Key Focus Elements |
KPO GOLDEN RULES and LIFE SAVING RULES
As part of the KPO HSE Policy on raising HSE cultural awareness and reducing incidents, KPO has three main Golden Rules (from 2017) and eleven Life Saving Rules (from 2019).
Golden Rules regulate the Company’s approach to Health and Safety: comply with legal regulations, intervene if in danger and respect colleagues while engaging.
Life Saving Rules are based on rules of the International Association of Oil and Gas Producers – IOGP, and are created as part of standardization of global health and safety regulations among oil and gas industry organizations, as well as to improve sharing of knowledge, experience and lessons learned. These rules focus on 11 types of activities with highest potential risk.
Fig. 8. Types of activities with high potential risk
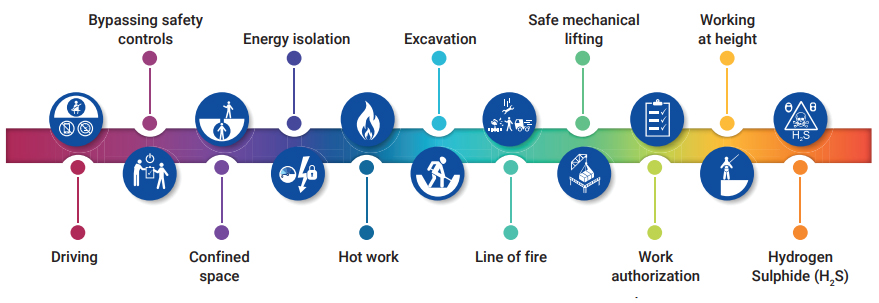
These set rules are applied to all employees of KPO, contractors and sub-contractors and all assets and production facilities operated by the Company.
In order to continue improving the personnel awareness on the Life Saving Rules, in 2021 a Life Saving Rules In-depth Learning campaign was launched including the training materials and tests to ensure effective understanding. Results obtained by the employees are:
- “Bypassing Safety Controls” test – completed successfully by 3,589 employees;
- “Line of Fire” test – completed successfully by 3,571 employees.
Consequences management
KPO has an HSE Behavioral Accountability and Consequence Management Model ensuring systematic study of employee’s behavior with either positive or negative consequences, and identifying appropriate reward or action.
In 2021, activities on raising awareness of the Company and contractor employees were continued via Skype. 90 % of high and medium risk contractors were covered. Awareness sessions on HSE Behavioral Accountability and Consequences Management Model will be continued for KPO Management staff, so that Managers support implementation of Consequences Management Model across the Company.
HSE Leadership and Culture
HSE Leadership and Culture Programme was developed to reinforce health and safety continuous improvement and to develop and enhance the skills of frontline supervisors to enable them to coach frontline workers to implement safe working practices.
The Programme’ implementation continued in 2021. “Coaching, involvement and intervention” courses were organized for the Well Operation department, Project Execution Directorate and their contractors. Also, with the support of the Corporate Safety Department, KMG-Parker Drilling Contractor initiated the Coaching Tool Pusher “Stop Work” Programme amongst its employees. The Corporate Safety Department, at the initiative of the Social Projects Department, held introductory mini-sessions on coaching, involvement and intervention for supervisors of the Social Projects contractors in Uralsk.
Management presence on work sites
For tracking the overall HSE performance and management interaction with employees at work sites, KPO practices HSE site tours at two levels: Management tours and Leadership tours engaging KPO Directors/Controllers, as well as Contractors’ management.
In 2021, the total number of HSE Leadership tours amounted to 127 compared to the planned 70 having resulted in 181 % plan completion.
Road safety
With a target to ensure more sustainable road safety performance, KPO continues implementing its Road Safety Improvement Plan. In 2021, the Company completed 90 % activities of the plan.
Key road safety achievements/implemented activities in 2021:
- Implementation of the new In-vehicle monitoring system (IVMS) parameters for both KPO primary and secondary logistics aligned with best international practice for further improvement of drivers’ behaviour;
- Driving competence assessment of more than 170 KPO and Contractors’ drivers both randomly and by applying risk-based approach, e.g. based on the IVMS RAG reports, vehicle type, load type, kilometres driven;
- Road traffic safety assurance review of 6 top low-performance contractors;
- Main Field roads potholes repair, road signs renewal, road marking;
- Arrangement of Winter road safety stand-down for KPO and contractors’ drivers on risks of driving in winter, including risk of hitting animals on the roads;
ISO 39001: Road Traffic Safety Management System – successful zero non-compliance pre-certification. KPO plans a certification on this standard in 2022.
HSE CULTURE
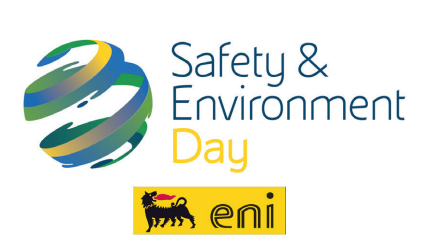
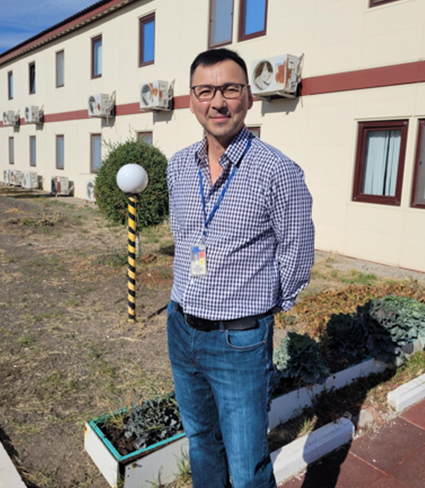
In 2021, a new HSE Communications Plan was introduced involving all HSE functions: Safety, Asset Integrity, Operations HSE, Projects Execution HSE, and Corporate Environment – in order to coordinate all HSE activities, including upcoming and current events, meetings, schedules. 97 % of the planned joint activities were implemented as per schedule.
As a part of the HSE Communications Plan, the KPO and Contractor Senior Management HSE Forum was held in December 2021. KPO Senior Management and representatives of 54 contractor companies participated in the Forum which was conducted in a hybrid format – some attendees were present offline in the Forum venue and others participated online. The purpose of the Forum was to jointly review HSE performance, experience and hold conversations about Safety culture and its elements, the level of Safety Culture ladder the Karachaganak project implements and what can we do in order to improve it.
The new “Learning from Incidents” database was rolled out in the past year where everyone can find Lessons Learnt archive both for internal (KPO) and external incidents, as well as useful Safety Moments for different HSE topics. It includes an advanced search engine which allows finding a particular case upon specific parameters (i.e. Related Life Saving Rules or types of injuries, activities, etc.).
In order to support and boost-up the KPO COVID-19 Vaccination Programme, the vaccinated employees were suggested to share their experience and their motivation to take the vaccine. All the stories were transmitted via pop-up messages on PC screens.
Together with Radio-Aksai we conducted a drawing contest amongst the kids of Aksai, dedicated to the International Day for Protection of Children, to make them think and talk about road safety. The award was held through radio and Instagram. In addition, the “Safety Starts at Home” presentation was rolled-out for review and discussion by KPO employees. It described the risks and hazards their kids could have faced in daily life, and what needs to be done to avoid adverse consequences of unsafe actions.