Asset Integrity
KPO monitors potential threats to its operations and mitigates Asset Integrity risks through its barrier management system. The Asset Integrity department together with the Units continuously assess the health status of the safety barriers to identify weaknesses, implement mitigating measures and establish plans to re-instate these barriers to its original design to prevent any major accident.
In order to minimize asset integrity risks, we have set a number of targets. The results of their implementation are presented further in the table.
2021 targets |
Target achievement |
Actions taken in 2021 |
Targets for 2022 |
Roll out a new Barrier Model tool and conduct awareness sessions for all KPO front line staff |
Done with further activities planned |
Rolled out the new Barrier Model tool as part of the Barrier Management Process. Conducted awareness sessions for key staff. Implemented the monthly review meetings with the Units. |
|
Continue the Process Safety Awareness campaign and develop an action plan based on the revised IOGP standards |
Done with further activities planned |
Updated the Process Safety Fundamentals Guideline and documentation as per the IOGP 2020 new release; launched PSF E-Learning and developed PSF videos. Distributed hand-out materials to KPO front line staff and contractors. |
Review the effectiveness of the implementation of the Process Safety Fundamentals |
Why is it important to us?
The main objective of Asset Integrity is to prevent major accidents and reduce the risks to people, environment, assets, and the Company’s reputation. It is an outcome of good design, construction, operating and maintenance practice.
Asset Integrity is achieved when facilities are structurally and mechanically sound and perform the processes to produce the products for which they were designed. Barriers that relate to the plants, people and processes are defined to reduce the risk for a major accident to a level that is as low as reasonably practicable.
he Asset Integrity Management Framework is a set of processes to prevent major accident hazards and to raise Asset Integrity and Process Safety awareness amongst the KPO employees, contractors and subcontractors working at the Karachaganak field.
The Asset Integrity Framework Management System consists of the following key processes:
- Barrier Management – through the application of a structured process supported by the using of the Barrier Model tool;
- Asset Integrity Performance Analysis – through the use of Key Performance Indicators;
- Management of Change system for Brownfield Modifications – through the use of the Management of Change database;
- Asset Integrity Assurance – through the use of reviews, audits, verifications and assessments;
- Asset Integrity Improvement Culture initiatives – through the production of e-Learning modules on the Mechanical Isolation Procedure, Process Safety Fundamentals and the Barrier Model process.
Within 2021, KPO has undertaken a number of activities addressing the key risks or barriers in the KPO asset integrity. In the table below, we present the completed activities in 2021 and the current status of the ongoing ones.
These completed activities allowed a reduction of the risk at Unit 3 and provided assurance on the robustness of some Process Safety process.
The activity currently ongoing will allow reducing the Process Containment and Ignition control risks field wide.
Tab. 20. Activities addressing the key risks or barriers in the KPO asset integrity
|
Barrier Impacted – finding and site place |
Continuous Improvement Activities in Asset Integrity |
ACTIVITIES COMPLETED IN 2021 |
Process Containment – 9 Vessel with integrity issue and Obsolete Flash Gas Compressors at Unit 3 |
Nine vessels were identified with integrity issues during the site inspection in the past years. These were replaced during Turnaround 2021. Flash Gas Compressors with integrity issues were identified as one of highest risk areas in Unit 3. They were taken out of service in 2021. |
Soft Barrier – Safety Critical Elements at KPC/KGDBN |
The KGDBN project at KPC has been completed and as part of the Handover to the Operations, the identification of the relevant safety critical element (SCE) of the KGDBN project has been carried out by a multidisciplinary team. |
|
Soft Barrier – Mechanical Isolation Procedure at Unit 2 and Unit 3 |
In order to verify compliance with the KPO procedures, an assessment was carried out on the Mechanical Isolation Procedure. |
|
Soft Barrier – Inhibits and Overrides procedure at Bolshoi Chagan, Atyrau Terminal, KPC and Unit 2 |
In order to verify compliance with the KPO procedures, an assessment was carried out on the Inhibits and Overrides procedure. |
|
ACTIVITIES STARTED IN 2021 ONGOING THROUGH 2022 |
Process Containment – Undersized pressure safety valve field wide |
A Safety review done by Engineering department highlighted potential undersized PSV’s in the facilities. The undersized PSV’s identified, mitigation action taken, design and procurement initiated, replacement scheduled for Turnaround 2022. |
Process Containment – Valves with banned materials field wide |
Site inspection ongoing to finalize the list of valves with banned materials. During the 2021 year several valves already changed out, remaining valves scheduled for replacement in Turnaround 2022. |
|
Ignition Control – EX Equipment field wide |
EX item review for all the facilities showed equipment with some gaps on the certification and maintenance. Site inspections completed, most critical items repaired/replaced, remaining scope being addressed. |
Barrier model
In 2021, the KPO Asset Integrity Department has worked on the new operational Barrier Management software tool. The new Barrier Model software was customized based on the KPO requirements in order to improve transparency and efficiency of the barrier management process with increasing use of “live data”. All new projects, upon completion, are put through the Barrier Model, such as the KGDBN project, which was delivered in 2021.
Loss of primary containment
Loss of Primary Containment (LOPC) is an unplanned or uncontrolled release of any material from primary containment, including non-toxic and non-flammable materials. The Annual Loss of Primary Containment Report for 2021 provides an analysis of the LOPC incidents that occurred during 2021 along with their defined recovery actions in terms of:
- Root causes (in accordance with Incident Investigation Tap Root Methodology),
- Level of compliance with Process Safety Fundamental rules,
- Status of corrective actions,
- Weeps & Seeps Leaks Register data.
Analysis of Process Safety Events is the key to prevent or reduce the likelihood and severity of Process Safety Events. Once a Process Safety event occurs, an investigation process is initiated, root causes are determined and recommendations are defined and followed up through the Synergi database.
Statistical analysis for 2019–2021 shows that the number of LOPC events decreased by 44.4 % in 2021 compared to 2020.
One Tier 1 Process Safety event occurred at KPC where a release of caustic soda solution splashed into the face of a KPO Lead Operator during the pressure leak testing activity. The injured person immediately used an eyewash in the safety shower and received first aid and further medical examinations; his eyesight was not impacted, however the sick list was issued.
No Tier 2 LOPC’s occurred in 2021. The number of Tier 3 LOPC’s was reduced from 17 in 2020 to 7 in 2021.
Graph 7. Loss of Primary Containment at KPO by process facilities, 2019–2021
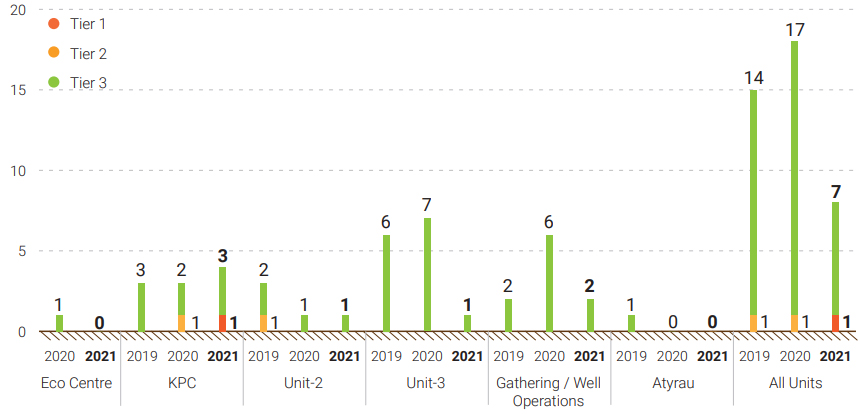