Occupational Health
In order to minimize risks and impact of the Company on occupational health, we have set a number of targets. The results of their implementation are presented further
Our 2021 targets |
Target achievement |
Actions taken in 2021 |
Targets for 2022 |
Continue with the implementation of the Workplace Mental Health and Well-being including:
|
Partially achieved |
|
|
Proceed with routine and unscheduled inspections of sanitary and living conditions at the contractors’ facilities |
Achieved |
Contractors’ welfare facilities were the focus of audits in 2021 as part of the Care for People Programme. Six audits were conducted. |
Support Project Execution and Industrial Relations divisions in conducting contractor welfare facility inspections particularly in relation to the planned Turnaround in September 2022 |
Implement the Fatigue Risk Management Programme in the Company |
Achieved |
Fatigue risk assessments were carried out and risk management plans developed by Project Execution Directorate, Transport and Security Departments. |
Continue implementing Fatigue Risk Management Programme across KPO. Special attention will be paid to Turnaround in 2022. |
Consider changing the concept of the Global Challenge programme in the context of current restrictions |
Not achieved, cancelled |
Global Challenge initiative was cancelled due to the COVID-19 pandemic. No plan to pursue the programme in 2022 as is. |
|
Install 10 automated external defibrillators (AEDs) |
Partially achieved |
Re-training of First Aiders was completed. 10 Automated External Defibrillators (AED) were purchased and installed in KPO offices in Aksai. |
Purchase further 10 automated external defibrillators (AEDs) install in the Field offices |
Purchase five units of Electronic Pre-shift Medical Examination System (ESME) and install them at all KPO sick bays |
Completed |
Seven units of ESME installed and operated within 2020–2021 in five KPO sick bays. ESME system is replacing manual pre-shift medical examination. Scope is BP, pulse, body temperature, breathalyser. Results are available for checking by supervisors online. |
|
Consider conducting an audit of the implementation of the Legionnaires’ disease risk reduction plan taking into due account the epidemiological situation |
Achieved |
The implementation status of the Legionella risk reduction plan was checked. The actions set in the Plan were implemented in most sites. |
Continue implementing requirements to prevent Legionella risks |
IMPROVING THE QUALITY OF EMERGENCY CARE
Emergency care preparedness and quick response are crucial in KPO.
KPO Medical Support team has established a system of Emergency Response of 24 hours provision of emergency pre-hospital care for the employees. Provision of pre-shift medical examination for employees and availability of 4 sick bays is arranged to reduce health, safety and environment risks in the field work environment.
Tab. 16. Healthcare deliverables in 2021
Medical Support Indicators 2021 |
|
Number of patients visited clinics |
1,075 |
Number of patients transported to medical facilities |
49 |
Number of exercises and drills participated |
274 |
First Aid training provided to employees |
230 |
Number of medevacs / repatriations |
1 |
Pre-shift medical examinations (drivers / operators / electricians) |
|
Number of examinations |
90,479 |
Cases of unfitness to work |
9 |
Random alcohol tests |
977 |
Positive random alcohol test results |
5 |
Medical Support Emergency indicators |
|
Number of emergency calls |
49 |
Why is it important to us?
Occupational health is very important, not only because we spend almost one third of our life at work and workplace factors impact our general health, but also because of an interaction between non-occupational illness and our ability to work.
KPO has a transparent Fitness to work procedure that prevents bias or discrimination. As a responsible employer, KPO pays great attention to complying with statutory requirements in regards to fitness to work of its employees. Using the pre-employment medical examination as a baseline, we monitor our people’s health both in terms of their ability to continue working and of any impact on their general health.
The aim is to prevent and mitigate any negative impact of the workplace factors. This is achieved by providing and maintaining safe work environments, modifying workplaces to fit the worker or reassigning them to other jobs, and, finally, by referring them to specialist care.
Health Department activities during the COVID-19 pandemic
For the period from January to September 2021, 88 patients with COVID-19 were monitored by medical personnel in the KPO medical facility at Czech Camp. 53 patients with COVID were evacuated from their workplaces in Aksai and the Field. PPE (masks, gloves, hand-sanitizers) was provided to all KPO employees on a monthly basis.
The COVID Care Team consisting of Health Department staff and volunteers from other departments continued helping the Company in its efforts to manage the pandemic’s impact.
KPO and Contractors conducted over 170,000 PCR tests in 2021. It helped control the spread of disease in the workplace and community.
During 2021, the Sanitary Laboratory has conducted 47 inspections throughout the Company facilities to check compliance with infection control measures.
Disinfection of workplaces after the COVID cases was arranged by outsourcing the activity.
Vaccination Programme
In 2021, KPO supported the RoQ vaccination efforts against COVID-19 by setting up a Vaccination Centre at the Aksai Hospital. More than 94 % of eligible employees have been fully vaccinated. This was achieved thanks to using a range of tools:
- Communication and education (dedicated webpage, “Ask the Doctor” sessions, posters, banners and pop-up messaging, vaccination stories, etc.);
- Exemption from PCR testing for the vaccinated;
- Lottery with valuable gifts;
- Bonus for achieving the vaccination targets.
Aksai Hospital Upgrade Project
The Aksai Hospital Upgrade Project was launched in January 2020, with the aim to upgrade the Aksai Hospital’s emergency and intensive care capability by achieving international standards within five years (2020 – 2025) via the KPO’s Social Infrastructure Projects. It includes improvements in equipment and infrastructure, as well as development of competence, and management systems.
Good progress was demonstrated on project delivery, as well as a significant impact on objective health outcomes (e.g. surgical mortality rates, and overall mortality rates). Positive case reports actual lives saved from new techniques and protocols. There was an overwhelming positive response from the medics and local community on social media.
The co-operation between KPO Health team, the Health Department of the WQO Akimat and the management of the Aksai District Hospital steer the activities of a joint effort for the benefit of the Burlin District’s community and KPO. The Project is overseen by the Joint Operators’ Oversight (JOO) comprised of health experts that had been established through the joint provision of technical advice to support achieving the goal.
MANAGEMENT OF ILL HEALTH
Medical insurance
A medical insurance benefit is offered to KPO employees that covers medical services in addition to those available through guaranteed free health care and mandatory medical insurance. Health insurance covers a range of services, from outpatient care to inpatient care and reimbursement of medicines and dental services. Employees with chronic conditions are referred to medical surveillance for regular check-ups and treatment.
Automated external defibrillators
In a cardiac arrest, chances of survival are reduced by 10 % every minute of delay. In KPO, delays to defibrillation can be as long as 15 minutes. Automated External Defibrillators (AED) allow First Aiders (i.e. trained laypersons) to defibrillate the patient. In 2021, the following activities were implemented:
- Re-training of KPO First Aiders completed;
- 10 AEDs are purchased and installed in Aksai-based KPO offices;
- Budget for more AEDs is requested.
Electronic System of Medical Examination
Electronic system of medical examination (ESME) – the project of digitalization and optimization of the process of pre-shift medical examination, which will replace the manual examinations. In 2021, ESME units were purchased and installed in five KPO clinics.
Absenteeism monitoring
In 2021, absenteeism at KPO was slightly down from the previous year.
Graph 5. KPO absenteeism rate, 2015–2021
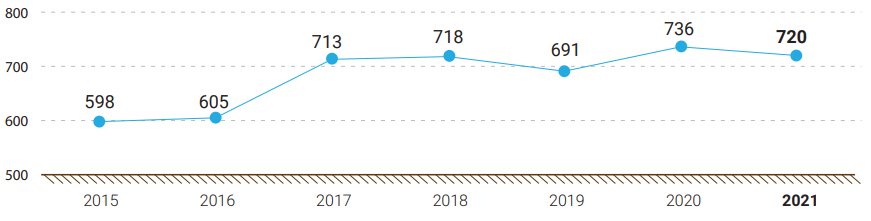
Note: KPO uses the following method to calculate the absenteeism rate:
- Absenteeism rate = actual number of days lost due to absence from work (due to illness) x 100/total number of employees. No information about the days of absence from the workplace for other reasons is available.
- KPO has adopted a methodology for calculating absenteeism by the number of employees (but not man-hours), since this methodology is a regulatory requirement.
Occupational diseases
Oil and gas industry features various occupational hazards (hydrogen sulphide, chemical reagents, noise and vibration, climatic factors, biological and psychosocial factors, etc.) that require identifying, assessing and managing associated health risks. These processes in KPO are well established and provide robust control mechanisms.
During 2021, Health risk assessments were carried out at Eco Centre. The results were used to prepare a corrective action plan that was handed over for implementation.
In 2021, there were no occupational diseases registered among KPO employees.
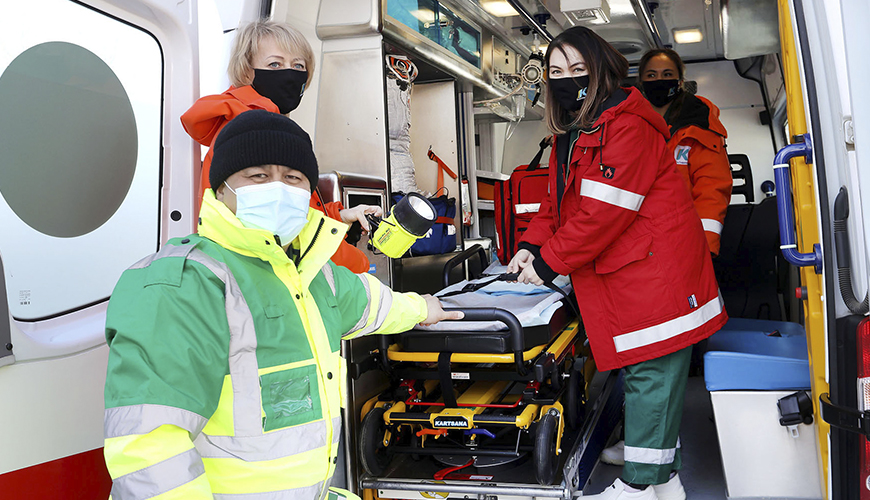
Fitness to work
Through pre-employment fitness to work assessments (FTW) providing a baseline and periodic medical examinations monitoring for any adverse changes, KPO strives to ensure that employees can complete tasks safely, without unacceptable risks to themselves, the Company or a third party.
The relevant Republic of Qazaqstan regulations as well as International Association of Oil and Gas Producers (IOGP) guidelines provide the legal and technical framework for KPO’s Fitness to Work procedure.
One of the key elements is the provision for employees of access to an appeal process in cases where they are unsatisfied with their FTW evaluation outcomes.
PROMOTION OF HEALTHY LIFESTYLE
Employee Assistance Programme
Employee Assistance programme is aimed at preventing harm to KPO employees arising from mental health problems, such as anxiety, depression, self-harm and suicides.
The programme involves confidential consultations by qualified third-party psychologists using multimedia, video, or face to face sessions available 24/7 via a set hotline. The programme also offers group sessions, lectures, discussions, and mental health education. Urgent psychological support is provided in cases of post-traumatic stress disorders resulted from a disaster, multiple casualty accidents, terrorism or other.
Fatigue Risk Management
Fatigue is a lack of mental alertness arising from lack of sleep. The oil and gas industry has a number of characteristics, which can contribute to fatigue.
In 2021, the results of pilot application of the FRM were considered in planning of drivers’ work schedules by Transport department. KPO has implemented a Fatigue Risk Management Procedure that outlines the management processes that minimise the risks of work-related injury or incidents due to fatigue.
OPERATIONAL CONTROL OF INDUSTRIAL FACILITIES
Both a statutory requirement, and one of the staples of industrial hygiene, sanitary compliance monitoring is conducted in KPO production facilities. Table 17 shows the monitoring data for the last three years.
Every case of non-compliance with the regulatory limits is analysed and relevant actions are taken. For example, fluorescent lamps that were responsible for low lighting levels started being phased out.
Noise is intrinsic in production facilities such as compressor houses. The Hearing Conservation Programme implemented in KPO is an example of control measures aimed at reducing worker exposure to excessive noise.
Workplace attestation
Statutory attestation of production facilities, which is conducted every five years, is aimed to evaluate working conditions.
In 2021, attestation of Eco centre was carried out by a licensed contractor company. 14 jobs were evaluated, of which 5 were graded as harmful. Corrective action plans were prepared following the outcomes of the attestation and submitted to the responsible persons for further actions. In 2022, large facilities such as KPC, Unit 2 and Unit 3 are due for the attestation.
Tab. 17. Monitoring of physical factors, 2019–2021
Occupational hazards |
2021 |
2020 |
2019 |
|||
No. of measurements |
No. of non-conformances |
No. of measurements |
No. of non-conformances |
No. of measurements |
No. of non-conformances |
|
Noise |
368 |
83 |
398 |
110 |
440 |
114 |
Vibration |
63 |
12 |
63 |
15 |
78 |
25 |
Electromagnetic fields |
3,676 |
50 |
3,500 |
35 |
4,164 |
36 |
Electrostatic fields |
2,048 |
0 |
1,737 |
0 |
2,322 |
0 |
Lighting |
2,743 |
730 |
2,861 |
660 |
3,085 |
703 |
Microclimate |
5,250 |
360 |
5,670 |
430 |
6,630 |
502 |
Workplace air |
12,342 |
0 |
11,607 |
0 |
15,741 |
0 |
TOTAL |
26,490 |
1,235 |
25,836 |
1,250 |
32,190 |
1,380 |